IDTechEx engineers know that re-entering a planet’s atmosphere is one of the toughest obstacles spacecraft face. During a return from low-Earth orbit, temperatures on the spacecraft can soar to around 1,600°C. For comparison, the Galileo probe that plunged into Jupiter’s atmosphere endured temperatures exceeding 16,000°C.
To withstand such extreme heat, the spacecraft’s heat shield must protect onboard systems, equipment, and, in some cases, astronauts. At the same time, the shield must remain lightweight to maximize the payload capacity.
The report “Heat Shields & Thermal Protection Systems for Spacecraft 2025-2035: Technologies and Market Outlook” by IDTechEx provides an in-depth analysis of the thermal protection systems (TPS) industry, covering everything from advanced ablative materials to innovative inflatable heat shields.
A New Era in Space Exploration
Space travel has evolved significantly over the decades. In the 20th century, exploration was dominated by government agencies like NASA, Roscosmos, and ESA. These institutions led efforts ranging from satellite launches to manned moon missions and robotic probes sent to distant planets.
Government space programs still lead in research and exploration, but private companies have transformed the industry. The rise of commercial operators has introduced new economic priorities, though many technical challenges remain the same.
Companies like SpaceX and ULA focus primarily on providing space launch services. Their clients include satellite operators, research organizations, and government agencies. For many missions, payloads such as satellites are designed for one-way trips and burn up during re-entry. However, there is increasing interest in technologies that support both launches and returns, especially as companies look to reuse spacecraft components to reduce costs.
The IDTechEx report examines the state of the TPS industry, highlighting the performance metrics and manufacturing challenges associated with different systems. It also explores how market trends are shaping both research and development.
SpaceX and the Evolution of Tile-Based Systems
Thermal tiles are a key component of spacecraft protection due to their low thermal conductivity. NASA first developed these tiles for the Space Shuttle program, aiming to create a reusable spacecraft. However, maintaining the Shuttle’s heat shield proved expensive and time-consuming, making rapid reuse difficult. Tragically, damage to a single tile caused the loss of Space Shuttle Columbia in 2003.
SpaceX has chosen to use a tile-based system for the upper stage of its Starship vehicle. Changes in the spacecraft’s geometry and the use of stainless steel instead of aluminum in its structure have influenced the design and requirements of its thermal protection system. The IDTechEx report details these design choices and explores advancements in tile technology, such as improved coatings and composite materials like TUFROC.
Ablative Systems: Handling Extreme Conditions
When re-entry conditions exceed what tiles can handle, ablation-based systems are often used. Ablative heat shields are designed to handle higher entry speeds and heavier payloads, but they are typically not reusable. These systems work by converting heat into gas during re-entry, dissipating it away from the spacecraft.
Ablators are critical for missions that involve extreme conditions, such as returning manned spacecraft from the Moon or entering outer planetary atmospheres at high speeds. The IDTechEx report discusses major types of ablative materials, such as AVCOAT and PICA, along with their manufacturing processes, material compositions, and performance characteristics.
It also addresses challenges such as the decline in rayon production, which affects carbon phenolic heat shields, and explores innovations like 3D-woven systems.
Inflatable Heat Shields: A Growing Innovation
Inflatable and expandable heat shields are a newer approach in thermal protection design. These systems aim to increase the heat shield’s surface area during re-entry, reducing its ballistic coefficient. This method requires advanced materials and manufacturing techniques, such as using aerogels for insulation.
Although still in the early stages of development, inflatable heat shields hold promise for applications like booster recovery and low-Earth orbit cargo returns. Challenges remain, including the need for onboard gas-generation systems. A European startup plans to test an inflatable aerodynamic decelerator in 2025, marking the first commercial attempt at this technology.
The Future of Thermal Protection Systems
As the space economy continues to grow, thermal protection systems will play an increasingly important role in enabling both cargo and crew returns. The IDTechEx report provides a detailed analysis of the market, covering the technical hurdles and key TPS categories under development. It also offers insights into how demand for materials and market value may shift over the next decade, reflecting the changing needs of the space industry.
About IDTechEx
IDTechEx provides trusted independent research on emerging technologies and their markets. Since 1999, we have been helping our clients to understand new technologies, their supply chains, market requirements, opportunities and forecasts. For more information, contact research@IDTechEx.com or visit www.IDTechEx.com.
Related News:
China’s Meridian Project Develops Mega Network for Space Weather Forecasting
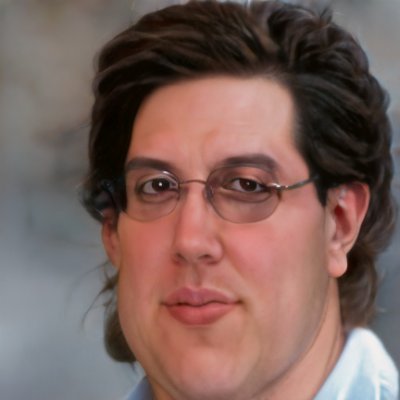
Geoff Thomas is an award winning journalist known for his sharp insights and no-nonsense reporting style. Over the years he has worked for Reuters and the Canadian Press covering everything from political scandals to human interest stories. He brings a clear and direct approach to his work.